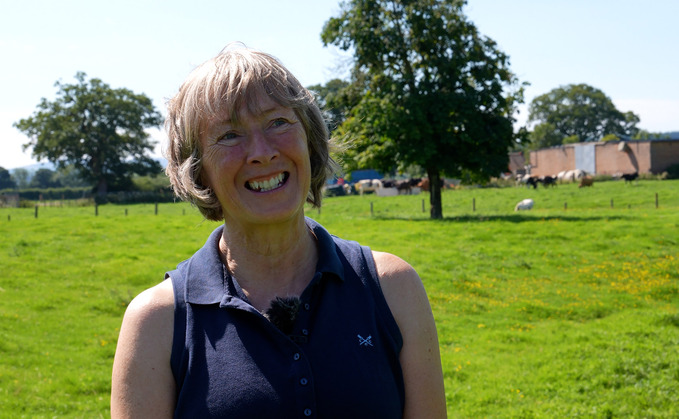
Mandy Stoker is a recipient of the School of Sustainable Food and Farming share of financial support which was awarded to farmers wanting to develop a sustainable idea on farm.
WHEN energy costs skyrocketed and Mandy Stoker calculated it would cost nearly £2,000 to heat the water needed to milk feed calves every day, she knew something had to be done.
During spring block calving, Mandy and her daughter-in-law Annie needed about 1,000 litres of water to a temperature of about 35-40degC to feed newborn calves.
Mandy says: "We need this hot water every day to make up the milk and just to wash down the buckets and other things we use. "I always get quite frustrated because by the time I need the hot water it has gone because it has been used to wash down the parlour."
With water demand, costs and environmental impact in mind, Mandy looked to alternative options for water heating and struck upon the idea of utilising the natural heat generated by existing farmyard manure (FYM) to heat water.
It is this idea which impressed the judges of the Journey to Net Zero competition, who awarded funding to fabricate the heat exchange system at Hilley Farm in Shrewsbury.
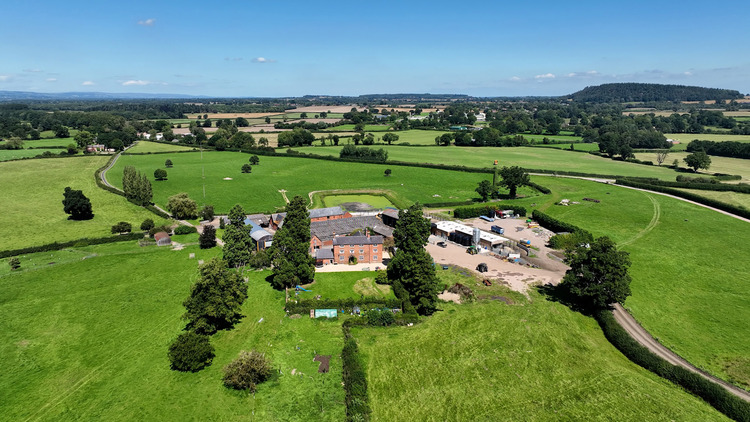
This summer, the Stokers constructed the system to see whether it could deliver on their requirements.
The Hot Stuff Project has proved successful, but various things have been learned along the way which will impact how the system is adopted next calving season:
1. Tank integrity can be a challenge
The standard 1,000-litre IBCs initially selected for the system proved too fragile to cope with the water pressure and weight of the compost. One of the six burst and the fittings on another broke.
As a result, when the system is reinstalled, 12,500-litre circular drums will be used instead.
2. It takes time to heat
It took about 24 hours for the water in the system to initially get above 30degC.
Mandy says: "It took a while for it to warm up as there was such a huge volume, but we had water coming out at 35degC. The more people run it, the colder it gets."
3. The system will need dismantling
The system will be dismantled once or twice a year and put back together with fresh FYM. This is a safety precaution due to the fact the buried tanks and pipes cannot be seen and the system is buried under manure which could be a contamination risk should anything break.
4. UV treatment is needed
An in-line chlorine dosing system and UV treatment will be added this season to ensure the water is fit for consumption. The water has been tested this season and it leaves the system the same quality as it goes in, but a treatment system will add a layer of protection.
5. The manure and water temperature may need to be managed
This year's trial run was carried out after calving and once the cows were out, which meant old manure was used.
Moving forward, fresh FYM (sawdust and straw) from the cubicles and loose yards will be used. Mandy suspects this will be hotter and will subsequently heat the water to a higher temperature. This could mean the water may need cooling. There may also be a risk of the manure catching fire in summer, so this will need to be monitored and cold water applied if necessary.
6. Location is important
The system is located on the edge of the building used to house the calves, which means water can be delivered by pipe to where it is needed.
Mandy says it would not be effective if water had to be transported to calves.
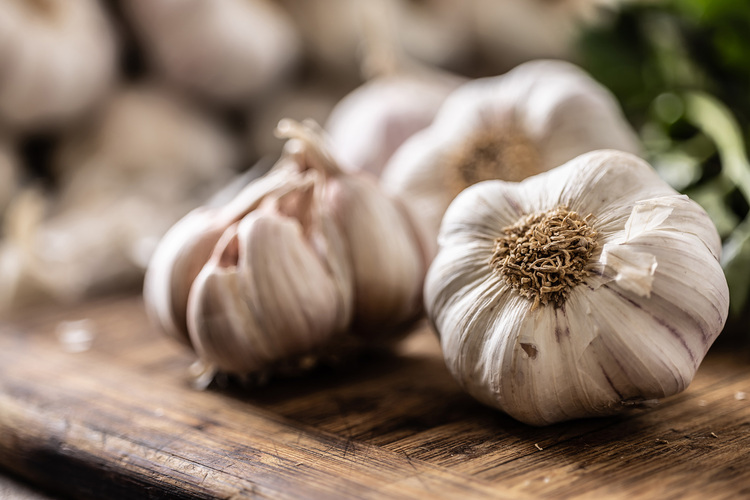
7. It has wider applications
As the project has proved successful, numerous other ways in which the heated water could be used has become apparent. This could include heating hot beds in polytunnels which could be used to grow garlic.
Mandy is keen to use homegrown garlic as a natural fly repellent when applied to cows' backs.
An area which is definite is how the hot water could be used to heat water for washing down the parlour. This fits with an overall drive to reduce dependence on external energy supplies and lower the business' carbon footprint.
Other steps which have been taken include installing solar panels, putting in clover and nitrogen fixing species and looking at integrated pest management. However, water heating and cooling of the milk remains one of the farm's biggest contributors to its carbon footprint.
As such, the plan is to use the hot water from the FYM system to heat parlour water during the time when calves are not being fed milk.
As the herd increases, Mandy expects to have about 400 calves a year and a requirement for a further 2,000 litres of hot water per day for cleaning.
As the water from the Hot Stuff system will likely be about 40degC when fresh manure is used, the water will only need to be heated by 40degC, which will require less energy than heating cold water from the tap. Mandy says: "So if we divert our [Hot Stuff] hot water into the cleaning system, we could potentially save more energy [about 40-50 per cent]."
Solar panels have also been installed since the competition entry, which should also help with energy savings.
HOT STUFF PROJECT: HOW IT WORKS
|
FARM FACTS
|
ABOUT THE JOURNEY TO NET ZERO COMPETITION THE Journey to Net Zero is a School of Sustainable Food and Farming competition, which was launched in summer 2022. A £50,000 funding pot was put up for grabs as part of the competition, which aims to help fund scalable, sustainable farming systems or processes which will have a positive and measurable impact on how the winners farm. More than 60 applied, with eight shortlisted for a Dragon's Den-style event at Harper Adams University - the home of the . Four winners were selected and were awarded grants of £10,000-£17,000. Their progress will be followed, with the aim of using their experiences to serve as wider learning for others in the industry.
|